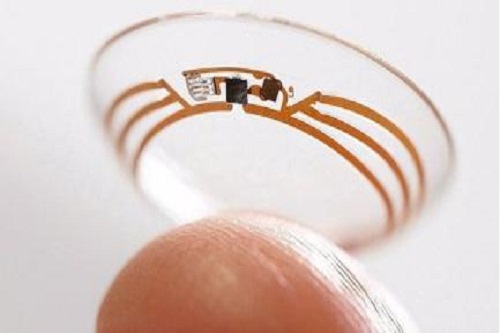
Intelligent technology combined with photoelectric detectors to see the light is not a dream
Just in February of this year, the company realized for the first time a modified version of its retina implant – IRISII with 150 electrodes. IRIS is only attached to the part of the implant outside the retina. It is mainly composed of tiny electrodes on the flexible circuit. The infrared photodetector unit and the small ASIC are responsible for multitasking and imaging related IR signals received by the photodetector. The electrode. Then, after these electrical signals stimulate ganglion cells, their terminals directly form the optic nerve fibers and transmit the sense signals to the brain.
The wearing part is in the shape of a goggle. It is equipped with a special event-based camera that processes visual information in front of the wearer and sends coded information through the glasses to IRIS. The built-in ASIC is wirelessly charged through two induction coils, one of which is located on the outer cover of the goggles.
IRIS implants were developed specifically for patients with retinitis pigmentosa (RP), a genetic disease that affects approximately 1 in 4,000 of the population, causing them to become blind before 40 years of age. The process of this implant takes about 2.5-3 hours, and it takes about a few weeks after the surgery to recover. Then you can start seeing the pattern. You can train the brain to understand the new vision and see a lot of simplified black and white. landscape. The training process involves identifying shapes, positioning light blocks on the screen, and sometimes using complete software to re-image the electrodes to the electrodes to accommodate areas of lower retina sensing.
Chief Executive Khalid Ishaque groomed: “The electrodes are not a limiting factor, but it is extremely complicated to send all the signals from the ASIC to the electrodes on such a narrow flexible foil. However, we cannot do this foil. Bigger because it makes the surgery more difficult. The bigger the gap in the patient's eyes, the greater the risk of suturing the scleral opening. In fact, the ASIC and the drive coil are just outside the eyeball. “We have managed more than a thousand electrodes through ASIC design, but it is still a challenge to further narrow the circuit on flexible foils,†he admitted, “but we can accelerate the pace in the next two or three years. Let IRIS contain more than a thousand electrodes."
Today, the company draws on the same visual input through a head-mounted ATIS sensor, and at the same time develops PRIMA retinal implants—a miniature modular array of wireless photovoltaic cells that can be implanted under the retina, while its electrodes are Bipolar cells located close to the eye. The time for surgical implantation of PRIMA may be less than one hour, and the risk is even lower because the implant will be built into the eye and no other control circuitry, wires or cables are needed.
PRIMA does not require the use of a multitasking ASIC. Ishaque explained that this photoelectric cell receives near-infrared (NIR) beams from the head-mounted glasses as input and sends electrical signals directly from its surface electrodes to the bipolar cells of the retina.
"For age-related macular degeneration (AMD), these cells still function," Ishaque pointed out. "By stimulating these cells so that this natural signal is mostly kept in contact with the optic nerve, we should be able to It's easier for the brain to find out which corresponds to visual stimuli, and without having to do much preprocessing or coding, it can also be said to enable faster learning."
AMD is a fairly common condition. There are more than 4 million cases in Europe and the United States, but patients are usually older and generally over 70 years old. This is why PRIMA can be treated with low-risk surgery, more favorably replacing IRIS. PRIMA is designed as a hexagonal photovoltaic cell (2 or 3 cells in series with one center electrode). The company has also designed different sizes of products from 140μm to 70μm.
"The average diameter of a bipolar cell is about 10 μm. Compared with the current way of stimulating ganglion cells with a larger electrode array, reducing the size of PRIMA, and the higher the picture density combined with local degeneration, is expected to achieve better stimulation effects. Let each pixel stimulate fewer cells.The coding of the signal will be different, and it is expected to use more physiological processing and network adjustment.The invisible NIR light will 'take' visual data from the sensor and send it to cover these. The center of the retina is modularized and the brain will read these new artificial signals," Ishaque said.
The PRIMA technology was originally developed by Daniel Palanker, a professor at the Stanford University School of Medicine and his research team, and they are now working on the development of 40-μm clusters.
If validated successfully, PRIMA will be able to enter a larger market for age-related macular degeneration (AMD), and it is expected to provide a more attractive price by implementing thousands of implants per wafer. PixiumVision has published a series of preclinical safety studies to date, and hopes to begin the first human feasibility study before the end of this year, followed by a large-scale focus trial in 2017.
“Because of the possibility of using thousands of electrodes, we are working on higher resolution visual acuity and facial recognition,†Ishaque commented. “Because AMD patients lose their central vision, our goal is to They bring artificial central vision."
In the end, PRIMA can even completely replace IRIS. Talking about stereo vision, Ishaque thinks this is a natural progression. "Once the technology is stable, we will have two sensors for the headset so that both eyes can handle it at the same time."
However, this start-up company does not want to stop here. "And the optic nerve in patients with glaucoma suppresses retinal signal transmission to the brain? Neuropathy or traumatic brain injury? What about the complete loss of the eye?" Ishaque asked. "In our global scientific and medical network, Not only are ophthalmologists and neurosurgeons connected to our eyes and brain -- from photons to neurons. The next step will be to directly stimulate visual cortical surfaces in the brain with visual signals, such as those of European Union (EU) research institutes and the U.S. Department of Defense. The DARPA is very interested in this research."
Cement-based non-shrinking self-leveling Grouting Material
KS series of grout is a high-tech one-component grouting material using Portland cement, pre-grade filler and additives that control the expansion in the plastic and can reduce water consumption.
Application of grouting Material:
Widely used in free-flowing precision grouting construction, including heavy machinery floor support, crane tracks and pillars foundation, but also can be used as mast, anchor bolt of the excellent reinforcement of grouting material; also is a good material for concrete repair works; design Beneath bridge supports, posts and flanged lamp posts, heavy pillar bases, and machine bases with dynamic loads. Such as thermal power plants, large paper mills, steel plant, steel mills, large machinery and equipment plants, cement plants.
Product advantages:
1, compensation shrinkage ---- gas expansion system, to compensate for shrinkage and settlement in the plastic slurry, to ensure that the grout material and the foundation in close contact
2, no chloride ---- The formula does not use chloride, thus avoiding the chloride hazards
3, high early strength ---- make the factory equipment faster to install and early use
4, non-ferrous ---- will not be rusty and stains or cracks due to rust expansion
5, reliability ---- factory pre-packaging materials, to eliminate the site produced by the error mixing
According to the standard:
KS series grouting material is based on the following part of the relevant standard test:
ASTMC-1107-97(Type)CRD-C621-82A
YB/T9261-1998 MS 522:part2:1989
ASTM C940-87 BS 4551:1980
JC/T986-2005
Expansion performance:
According to the American Standard ASTMC827 plasticizing stage test expansion rate of 0.5% or more, the long-term expansion of the curing stage to meet the requirements of the relevant standards.
Material properties:
project model |
KS-40 |
KS-60 |
KS-801 |
|||
40 |
401 |
60 |
601 |
|||
(mpa) compression strength(mpa) |
1 day |
20 |
22 |
25 |
30 |
45 |
28 day |
40 |
50 |
60 |
70 |
85 |
|
(mpa) Flexural strength(mpa) |
28 day |
9 |
10 |
12 |
12 |
12 |
Setting time |
Initial setting |
6.5h |
6.5h |
6h |
6h |
6h |
Final condensate
|
8h |
8h |
7.5h |
7.5h |
7.5h |
|
Expansion time |
Plastic stage |
Start 10min to initial setting |
Start 10min to initial setting |
Start 15min to initial setting |
Start 15min to initial setting |
Start 15min to initial setting |
Curing stage |
The final setting to cure more than 28 days |
The final setting to cure more than 28 days |
The final setting to cure more than 28 days |
The final setting to cure more than 28 days |
The final setting to cure more than 28 days |
|
Liquid density |
(kg/m³) |
2150 |
2150 |
2200 |
2200 |
2250 |
Water consumption |
Ks/dag |
3.8~4.0 |
3.8~4.0 |
3.8~4.0 |
3.8~4.0 |
3.6~3.8 |
1. floor grouting:
The flow distance should be determined based on the slit width and the liquid flow indenter to ensure that the grout flows from the gap to the front exit and the gap must not exceed 200 mm. If you guarantee a pressure head of 250mm, the maximum flow distance of up to 3 meters.
Note: The base surface must be constructed with oil-free and non-adherent loose material. If the surface of the concrete defects or slurry is cut intact before construction, the screw holes or solidified hole dust or sand blown net.
2. Floor:
Clean, no oil and other impurities must be removed to provide relief holes to ensure that all isolated areas are ventilated.
Pre-soaked: A few hours before grouting, the cleaned foundation must be submerged in water. Remove water from the free water and the hole just before pouring.
3. Stir:
To achieve the desired consistency, the amount of water must be accurate, the selected amount of water after slowly pouring it into the mixing vessel, while stirring feed, add complete package and continue stirring for 3-4 minutes until evenly dispersed, no knot Block phenomenon so far.
4. Grout:
The well-mixed material is poured over a period of 10 minutes to fully benefit from the expansion process. Each single perfusion thickness up to 200mm, the minimum width of the seam is 10mm.
5. Specific construction of large volume grouting:
Such as the thickness of more than 200mm. Aggregate grading (stones up to 10 mm in diameter) shall be added to the slurry to reduce the heat of hydration. The amount of aggregate used shall not exceed 1 part by weight of 1 part of KS series grout.
6.Low temperature construction:
When the temperature drops below 2 ° C, warm water (30-40 ° C) may be
used to accelerate the strength increase and the cementitious material
should be handled in winter.
High-temperature construction:
When the temperature exceeds 35 ℃, grouting material should be stored in a cool place, and cold water mixing.
Conservation:After grouting is complete, all exposed parts should be cured with Cask Cares or wet sacks.
Countermeasure :
KS series grout contains cement powder, which when mixed with gypsum or
when wet, releases alkali that is harmful to the skin. Avoid inhaling
dust and avoid touching the skin or eyes.
Estimation:pack
KS series grouting material) 25KG/bag
Under free flow the volume is about 13.0L
CONSTRUCTION schematic:
Storage:
KS series grouting material intact material in dry place storage period
of 12 months, if stored in high temperature and high temperature
storage area will be shortened.
Kasler Building Materials Co., Ltd.
guarantees the quality of its products manufactured and sold, and sells
it according to the agreed sales terms. Casper pledges to make every
effort to advise clients on the construction of the project,
recommending the use of solutions and materials. However, as we are
unable to exercise direct and continuous control over the use of our
products for sale, CASLUS BUILD MATERIALS CO., LTD can not afford to use
whatever advice our customers ultimately end up using and recommending
solutions and materials The use of the product caused by a variety of
direct or indirect responsibility.
Grouting Material
Grouting Material,Cement Grouting Material,High Strength Grouting Material,Non-Shrinkage Grouting Material
Jiangmen Kasole Building Materials Co., LTD. , https://www.kasole-paint.com